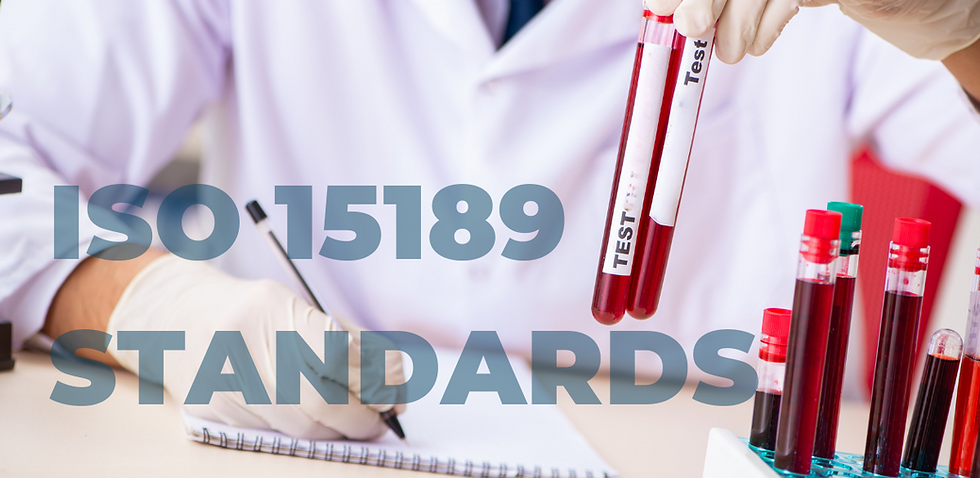
In the realm of laboratory operations, maintaining the highest standards of quality is paramount. A laboratory's Quality Management System (QMS) serves as the backbone of its operations, ensuring consistency, accuracy and reliability in processes and procedures. Guided by the principles outlined by esteemed organisations such as the Clinical and Laboratory Standards Institute (CLSI) and ISO 15189, laboratories strive to embody excellence across all facets of their operations. Let's delve deeper into the 12 essential components that comprise a robust QMS.
1. Organisation: Building a Foundation of Quality:
At the core of any successful laboratory is a formal QMS that fosters a culture of quality. From the management team to the quality unit, every individual plays a crucial role in upholding standards and ensuring consistency in procedures. The organisational structure should support ongoing monitoring and improvement of quality processes.
2. Personnel: Nurturing Talent and Expertise:
The most valuable asset of any laboratory is its personnel. Qualified and capable staff members form the cornerstone of quality operations. Through comprehensive training, motivation and engagement initiatives, laboratories empower their workforce to deliver excellence consistently. Documenting training processes within the QMS ensures transparency and accountability.
3. Equipment: Ensuring Reliability and Safety:
Every piece of equipment within a laboratory must be meticulously maintained to operate safely and reliably. From installation to calibration, stringent protocols govern the management of equipment. Monitoring suppliers' quality standards and adherence to calibration processes is imperative to uphold the highest quality standards.
4. Purchasing and Inventory: Safeguarding Supply Chain Integrity:
Effective supply chain management is critical to ensure the consistency and quality of raw materials and supplies. Proper inventory management practices verify the integrity of stored materials, safeguarding against contamination or degradation. Partnering with reputable suppliers who uphold rigorous quality management standards is essential for maintaining excellence.
5. Process Control: Guaranteeing Precision and Accuracy:
Process control lies at the heart of quality assurance in laboratories. From sample collection to validation, meticulous Quality Control processes ensure precision and accuracy in testing procedures. By adhering to standardised protocols, laboratories uphold the integrity of their results, instilling confidence in stakeholders.
6. Information Management: Securing Data Integrity:
Laboratories generate vast amounts of data, ranging from test results to patient information. Managing this information securely and accurately is paramount. Controlled access ensures confidentiality while facilitating accessibility for authorised personnel, thereby maintaining data integrity and compliance with regulatory standards.
7. Documents and Records: Establishing Standardisation:
Central to effective quality management are standardised documents and records, notably including Standard Operating Procedures (SOPs). These documents serve as the blueprint for processes, ensuring consistency and adherence to best practices. Accessibility, accuracy and security are fundamental principles governing document management within the QMS.
8. Occurrence Management: Detecting and Resolving Issues:
Inevitably, errors or non-conformances may arise within laboratory operations. A robust QMS facilitates the detection and resolution of such occurrences through comprehensive tracking and investigation mechanisms. By addressing root causes and implementing corrective actions, laboratories mitigate risks and uphold quality standards.
9. Assessment: Benchmarking Performance:
Regular assessment of laboratory performance against internal standards and industry benchmarks is essential for continuous improvement. Internal auditors and external inspectors play pivotal roles in evaluating processes and identifying areas for enhancement. By benchmarking against best practices, laboratories strive for excellence in all aspects of their operations.
10. Process Improvement: Driving Continuous Enhancement:
A hallmark of an effective QMS is its emphasis on continuous improvement. By integrating quality assurance, control and corrective actions, laboratories foster a culture of innovation and enhancement. Through systematic analysis and feedback loops, processes are refined, leading to heightened efficiency and quality outcomes.
11. Customer Service: Prioritising Stakeholder Satisfaction:
Ultimately, the success of a laboratory hinges on its ability to deliver exceptional customer service. Understanding and meeting the needs of stakeholders, including patients, healthcare providers and regulatory bodies, is of paramount importance. Incorporating customer feedback into quality improvement initiatives ensures that services align closely with stakeholder expectations.
12. Facilities and Safety: Upholding Standards of Excellence:
Ensuring a safe, secure and clean environment is non-negotiable for laboratory operations. Comprehensive procedures govern facility management, encompassing physical security measures, hazard containment protocols and ergonomic considerations. By prioritising worker safety and environmental stewardship, laboratories demonstrate their commitment to excellence.
In conclusion, a laboratory's Quality Management System is the cornerstone of its pursuit of excellence. By adhering to the 12 essential components outlined by industry standards, laboratories can uphold the highest standards of quality, reliability and integrity in their operations. Through continuous improvement initiatives and a steadfast commitment to customer satisfaction, laboratories position themselves as beacons of excellence in the ever-evolving landscape of healthcare and diagnostics.
Comments